Understanding Pressure Die Casting Suppliers: Your Comprehensive Guide
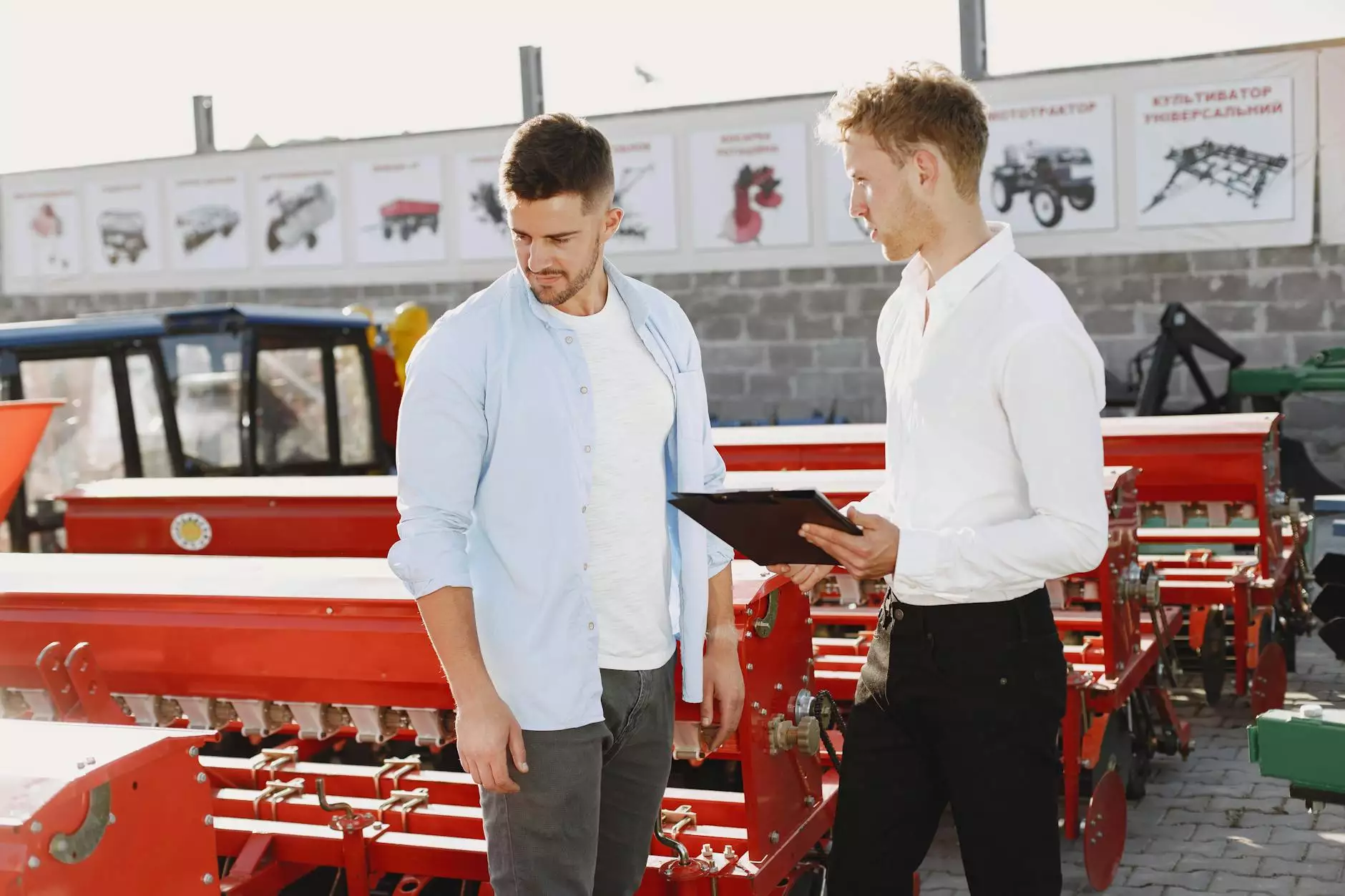
In the world of metal fabrication, the role of pressure die casting suppliers is crucial. These suppliers specialize in producing high-quality metal components for a variety of industries. In this article, we will dive deep into the processes, advantages, and considerations when selecting pressure die casting suppliers, ensuring that you have a thorough understanding of this essential aspect of manufacturing.
What is Pressure Die Casting?
Pressure die casting is a widely used manufacturing process that involves forcing molten metal into a mold under high pressure. This technique is commonly employed for producing large volumes of parts that require dimensional accuracy and high-quality surface integrity.
How Does Pressure Die Casting Work?
- Preparation: The process begins with the preparation of the die (mold). The die is usually made from high-strength steel and is designed to withstand the extreme conditions of the casting process.
- Heating: The metal, typically aluminum, zinc, or magnesium, is heated until it's molten. This molten metal must reach the correct temperature to ensure optimal flow into the mold.
- Injection: Once the metal is molten, it's injected into the mold at high pressure. The pressure ensures that the metal fills every cavity within the mold, capturing intricate details.
- Cooling: After the metal fills the mold, it’s allowed to cool and solidify. The cooling process is crucial for achieving the desired mechanical properties.
- Ejection: Once cooled, the die is opened, and the finished component is ejected. Any excess material or flashing is removed during this stage.
Advantages of Using Pressure Die Casting Suppliers
Collaborating with experienced pressure die casting suppliers offers numerous benefits:
- High Precision: Parts produced via die casting exhibit superior dimensional accuracy. This precision reduces the need for secondary machining processes.
- Mass Production: The die casting process is highly efficient for mass production, allowing companies to meet large-scale demand without compromising quality.
- Complex Geometries: With pressure die casting, manufacturers can create complex shapes and intricate designs that would be difficult, if not impossible, to achieve with other methods.
- Material Efficiency: The process generates minimal waste compared to traditional machining, making it both cost-effective and environmentally friendly.
- Enhanced Surface Finish: The parts produced often require little to no finishing work, resulting in lower post-processing costs.
Industries That Benefit from Pressure Die Casting
Many industries leverage the capabilities of pressure die casting suppliers to enhance their operations. Key sectors include:
- Automotive: The automotive industry utilizes die-cast parts for components like engine blocks, transmission cases, and various housings.
- Aerospace: Aerospace applications require high precision and lightweight components, making pressure die casting an optimal choice.
- Electronics: The electronics industry often requires casings and housings that need durability alongside aesthetic appeal.
- Consumer Products: Many everyday items, including appliances and tools, are produced using die casting technologies.
Choosing the Right Pressure Die Casting Supplier
When selecting a pressure die casting supplier, several factors should be taken into consideration:
1. Experience and Expertise
Choose a supplier with a proven track record in the industry. An experienced supplier will understand the nuances of the die casting process and how to handle various materials effectively.
2. Quality Assurance
Quality control is paramount in pressure die casting. Ensure your supplier adheres to international quality standards and has stringent testing and inspection processes in place. Look for certifications such as ISO 9001.
3. Technological Capabilities
Modern die casting relies heavily on technology. A supplier who invests in the latest machinery and software can offer enhanced efficiency, quality, and innovation.
4. Customization Options
Your needs may require customized solutions. Verify that the supplier can provide tailored molds and flexibility in production to meet specific requirements.
5. Reputation and Reviews
Research the supplier's reputation through reviews and testimonials from previous clients. A supplier with positive feedback is likely to be reliable and professional.
Case Study: DeepMould.net - Leading Pressure Die Casting Supplier
One prominent player in the field of pressure die casting suppliers is DeepMould.net. This company has established itself as a leader in the metal fabrication industry, offering high-quality die casting services tailored to various sectors.
The DeepMould Advantage
DeepMould.net distinguishes itself through:
- Innovative Solutions: They employ cutting-edge technology to ensure the precision and durability of all products.
- Dedicated Customer Support: Their team offers exceptional customer service, guiding clients through the entire process from design to production.
- Competitive Pricing: With transparent pricing models and cost-effective solutions, DeepMould ensures that high quality does not come at an exorbitant cost.
- Fast Turnaround Times: Efficiency in production and a streamlined process allows them to deliver products quickly, enabling clients to meet project deadlines.
Future Trends in Pressure Die Casting
The pressure die casting industry is evolving, and several trends are shaping its future:
- Adoption of Advanced Materials: As technology progresses, the use of advanced materials that provide higher strength-to-weight ratios is increasing.
- Automation: Increased automation in the manufacturing processes will lead to better precision and reduced labor costs.
- Sustainability Practices: Suppliers are focusing on sustainable practices, including recycling materials and reducing energy consumption in production.
- Integration with Industry 4.0: The rise of Industry 4.0 has brought more digital tools and IoT technologies into the manufacturing realm, improving efficiency and monitoring.
Conclusion
In conclusion, partnering with the right pressure die casting suppliers can significantly impact your manufacturing efficiency and product quality. By understanding the die casting process, recognizing the advantages, and being informed when selecting a supplier, you can ensure that your manufacturing needs are met with precision and excellence. For those looking for a trusted supplier, DeepMould.net stands out as a reliable choice, offering quality, efficiency, and innovation in metal fabrication.