The Vital Role of Injection Mould Companies in Metal Fabrication
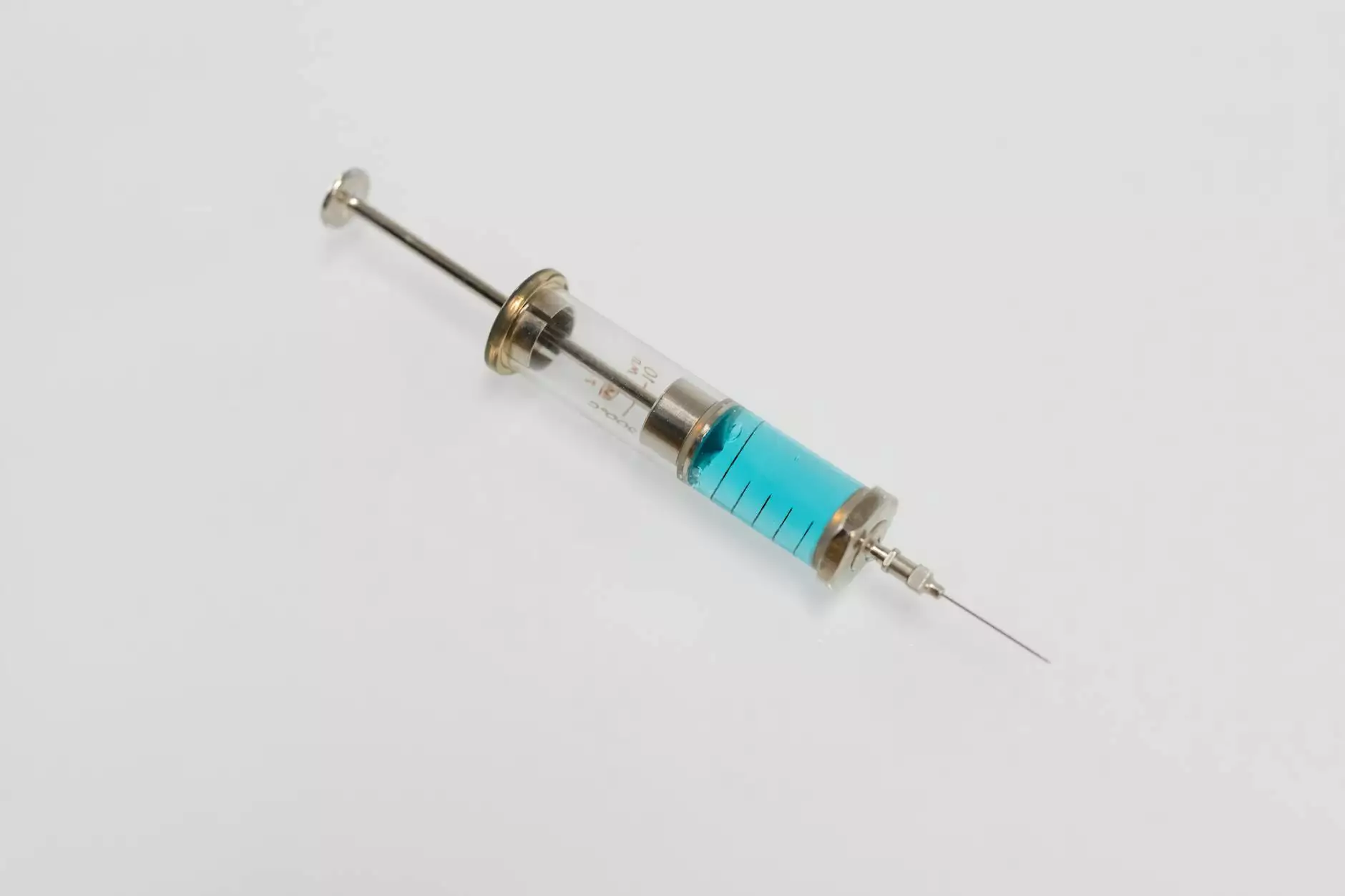
In today’s competitive manufacturing landscape, injection mould companies play a fundamental role in the success of industries that rely heavily on sophisticated and cost-effective production processes. With the rise of advanced technologies and the constant push for efficiency, these companies have become indispensable allies for manufacturers worldwide. This article delves deep into the inner workings of injection moulding, its significance in metal fabrication, and how it shapes the future of manufacturing.
What is Injection Moulding?
Injection moulding is a manufacturing process where molten material is injected into a mould to create specific shapes and components. It is widely used for producing plastic, metal, and other materials, making it a versatile option for diverse industries. The process begins by heating a material until it becomes pliable, followed by injecting this material into custom-made moulds that shape the final product. Once cooled and solidified, the moulds are removed, revealing precisely crafted components.
The Process of Injection Moulding
The injection moulding process consists of several key stages:
- Designing the Mould: This initial step involves creating a detailed design of the mould, tailored to the specific component that needs to be produced. Computer-aided design (CAD) software is often used to ensure precision.
- Material Selection: Depending on the application, various materials can be used, including metals, plastics, and composites. Each material has its unique characteristics, so selecting the right one is crucial.
- Heating the Material: The selected material is heated until it reaches a molten state. This is usually done in an injection unit, ensuring consistent flow and temperature.
- Injection: Once the material is molten, it is injected into the mould under high pressure, ensuring that it fills all the cavities of the mould.
- Cooling: After injection, the material is allowed to cool and solidify inside the mould, taking on its final shape.
- Demoulding: Once cooled, the mould is opened, and the finished component is ejected.
- Finishing Touches: Post-production processes may include trimming, painting, or additional machining to ensure the final product meets quality standards.
The Advantages of Working with Injection Mould Companies
The association with injection mould companies offers a plethora of advantages for businesses involved in metal fabrication:
- Efficiency: Injection moulding significantly speeds up production times, allowing for the rapid manufacturing of large quantities of parts without sacrificing quality.
- Cost-Effectiveness: While the initial investment in mould design and production can be high, the long-term savings associated with reduced material waste and labor costs make it more economical.
- Complex Geometries: Injection moulding allows for the creation of complex shapes and intricate designs that might be tough or impossible to achieve through traditional machining methods.
- Consistency and Accuracy: High precision designs ensure that each part produced is consistent in quality and specifications, thus maintaining the integrity of the product.
- Material Versatility: From metals to plastics and beyond, injection moulding supports a diverse range of materials, catering to various industry needs.
The Impact of Injection Moulding on Metal Fabrication
In the realm of metal fabrication, injection moulding presents unique opportunities and challenges:
Applications in Metal Fabrication
Metal fabrication encompasses a variety of processes, and injection mould companies have carved a niche in several key areas:
- Automotive Industry: Injection moulding is widely utilized to produce components such as gear knobs, panels, and various intricate parts needed for vehicle assembly. This not only helps in reducing the weight of the vehicles but also enhances fuel efficiency.
- Aerospace Manufacturing: Components for aerospace applications require superlative precision and durability. Injection moulding technology allows for producing lightweight yet robust parts that meet stringent industry standards.
- Electronics: From housings to connectors, the electronics industry often relies on injection moulding to create reliable and high-quality components that protect sensitive electronic systems.
- Medical Devices: With an increasing focus on precision and safety in the healthcare sector, injection mould companies provide tailored solutions for designing and manufacturing critical medical devices.
Choosing the Right Injection Mould Company
Selecting the right injection mould company can be a critical decision for any business. Here are some factors that should be considered:
Experience and Expertise
Experience in the industry often translates to better design capabilities, production techniques, and understanding of market demands. Look for companies with a proven track record in your specific industry.
Technological Capabilities
Today’s manufacturing environment demands the latest technologies for efficient production. Assess whether the company utilizes advanced equipment, such as robotic systems for automation, to enhance precision and productivity.
Material Knowledge
Injection mould companies should have extensive knowledge regarding the properties and applications of various materials. This knowledge helps in advising on the best material choices for specific projects, ensuring optimal performance and durability.
Quality Control Processes
Ensure that the company implements strict quality control measures throughout the production process. Certifications such as ISO can be indicative of a company's commitment to quality.
Customer Support
Evaluate the level of customer support offered. A responsive and knowledgeable team can help navigate any challenges that arise during the production process.
Future Trends in Injection Moulding
The field of injection moulding is evolving rapidly, driven by technological advancements and changing market needs. Here are some trends to watch:
- Industries 4.0: The integration of smart manufacturing techniques, including IoT and AI, is revolutionizing the injection moulding process. Companies are becoming more data-driven, enabling precise process control and improved efficiency.
- Sustainability: In an era where sustainability is crucial, injection mould companies are producing environmentally friendly materials and processes, including recyclable plastics and reduced waste strategies.
- 3D Moulding Technology: The introduction of 3D printing into mould design is providing unprecedented design flexibility and rapid prototyping capabilities.
- Customization: As consumers demand more tailored products, injection mould companies are adapting their methods to provide greater customization options.
Conclusion
Overall, injection mould companies are integral to modern metal fabrication and manufacturing processes. Their ability to produce high-quality, consistent, and complex components makes them invaluable partners for industries ranging from automotive to electronics. As technology continues to advance, these companies will play a pivotal role in shaping the future of manufacturing, driving efficiency, sustainability, and innovation. Investing in strong partnerships with top-tier injection mould companies can provide businesses with the competitive edge needed in today’s fast-paced market.
For businesses aiming for excellence in manufacturing processes, collaborating with a reputable injection mould company like Deep Mould can unlock new potentials and enhance product offerings significantly.