Industrial Vacuum Systems: The Backbone of Efficient Manufacturing
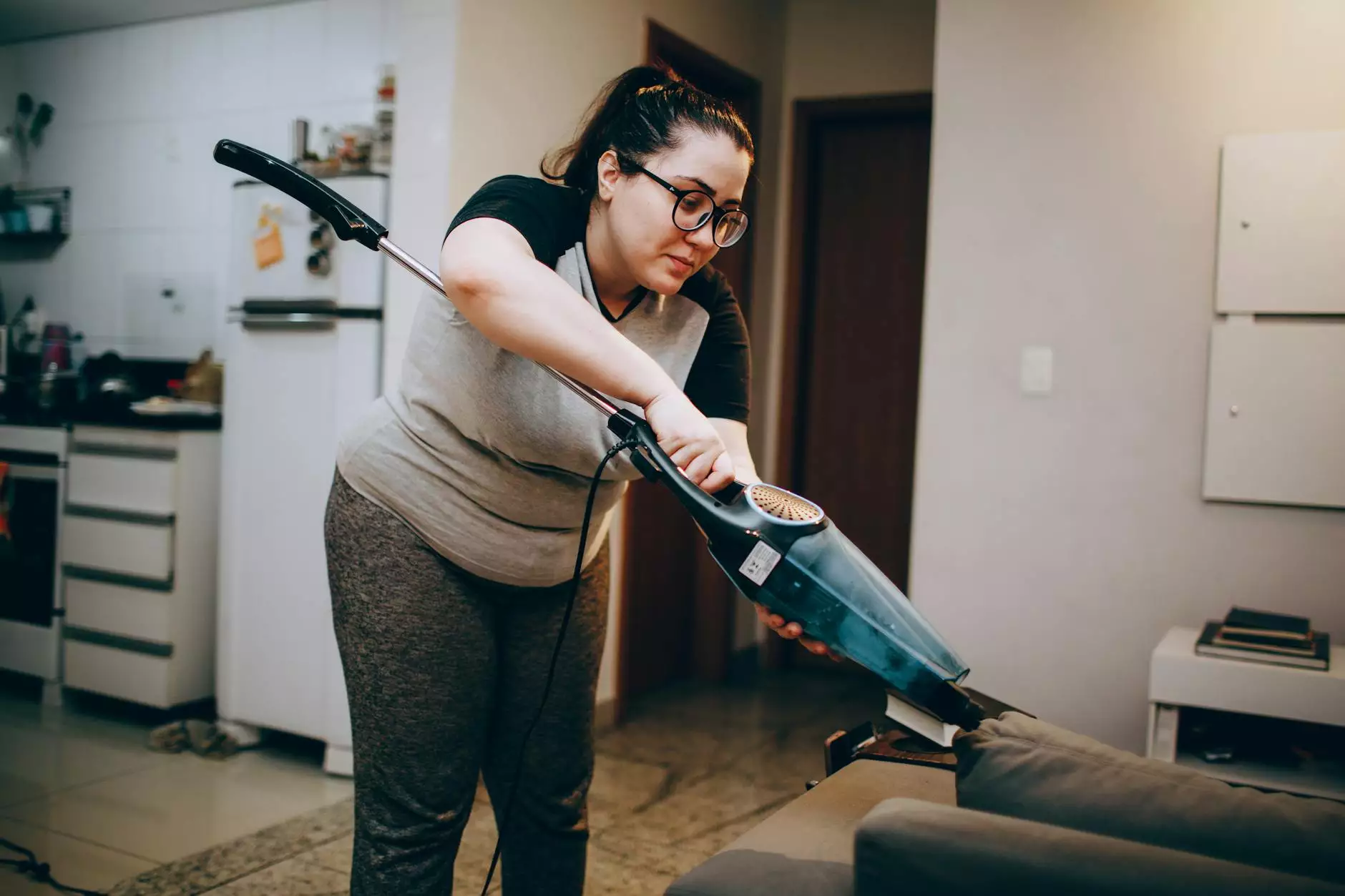
In today's fast-paced industrial landscape, businesses are continuously seeking ways to enhance productivity, improve safety, and maintain quality standards. One of the critical components that facilitate these goals is industrial vacuum systems. These systems play a pivotal role in ensuring a clean and efficient operational environment, which is vital for maintaining high standards in the manufacturing process.
The Importance of Industrial Vacuum Systems
Industrial vacuum systems are specially designed to handle a wide variety of applications in various industries, ranging from automotive to food processing. This article explores their significance, types, applications, and the benefits they provide to modern manufacturing operations.
Understanding Industrial Vacuum Systems
At the core of effective manufacturing lies the understanding of industrial vacuum systems. These systems are engineered to remove dust, debris, and other unwanted materials from the production floor. They serve not only to create a safer working environment but also to protect expensive machinery from damage caused by the accumulation of particulates.
Types of Industrial Vacuum Systems
There are several types of industrial vacuum systems, each tailored to specific needs within an industrial setting. Understanding the various designs and their applications can help businesses make informed decisions about which type best fits their operational requirements.
- Centralized Vacuum Systems: Suitable for larger facilities, these systems provide vacuum power to multiple production areas through a network of pipes. This design minimizes maintenance and increases efficiency.
- Portable Vacuum Systems: These are versatile units that can be moved around the facility, making them ideal for cleaning specific machines or locations without being permanently installed.
- Stationary Vacuum Systems: Fixed units connected to specific machines or processes, stationary systems are great for applications that generate high volumes of debris or dust.
- Explosion-Proof Vacuum Systems: Designed for environments where flammable dust or vapors are present, these systems are engineered to prevent any risk of ignition and ensure safety compliance.
Applications of Industrial Vacuum Systems
The best features of industrial vacuum systems come to light when examining their applications across various industries. Here are some common areas where these systems are essential:
1. Manufacturing and Fabrication
In manufacturing, industrial vacuum systems are used to collect metal shavings, wood dust, and other debris generated during fabrication. This keeps the workspace clean and minimizes the risk of accidents.
2. Pharmaceutical Industry
In the pharmaceutical sector, the cleanliness of the production environment is paramount. Industrial vacuum systems help in maintaining sterile conditions by efficiently removing dust and contaminants.
3. Food Processing
Food safety is a top priority in food processing plants. Vacuum systems assist in the removal of food particles and packaging debris, helping maintain hygiene standards.
4. Textile Industry
The textile industry generates lint and fiber waste that can accumulate rapidly. Industrial vacuum systems are crucial in keeping the workspace clear of these materials, thus preventing fire hazards and equipment damage.
Benefits of Utilizing Industrial Vacuum Systems
Implementing industrial vacuum systems in a business setup offers several compelling advantages:
1. Enhanced Safety
By effectively removing hazardous debris and pollutants, these systems help ensure a safer working environment for all employees. This reduces the risk of slips, trips, and falls caused by accumulated waste.
2. Improved Efficiency
By keeping production areas clean and free from contaminants, industrial vacuum systems increase operational efficiency. Machinery operates better and is less likely to encounter downtime due to maintenance caused by accumulated waste.
3. Compliance with Regulations
Many industries are subject to strict regulations regarding cleanliness and safety. Utilizing an industrial vacuum system helps businesses comply with these regulations, avoiding costly fines and shutdowns.
4. Cost Savings
While there is an initial investment in industrial vacuum systems, the long-term savings on maintenance, reduced downtime, and increased productivity often outweigh the costs. Furthermore, by protecting equipment, these systems contribute to extended machinery life.
Choosing the Right Industrial Vacuum System
When it comes to selecting the most suitable industrial vacuum system for your business, several factors should be considered:
- Volume of Debris: Assess the volume and type of debris your operations generate to determine if you need a portable or centralized system.
- Environment: Consider if the system will be used in a hazardous environment. If so, look for explosion-proof options.
- Space Considerations: Evaluate the layout of your facility to determine where vacuum systems would be most effective.
- Budget Constraints: Establish a budget that will allow for the purchase of a quality system while keeping long-term savings in mind.
Maintenance of Industrial Vacuum Systems
Like any equipment, industrial vacuum systems require regular maintenance to ensure optimal performance:
1. Regular Inspection
Schedule routine inspections to check for wear and tear on hoses, filters, and motors. Early detection of issues can prevent costly repairs down the line.
2. Filter Cleaning and Replacement
Filters should be cleaned or replaced regularly, depending on the system's usage. Clogged filters can diminish vacuum efficiency and potentially contaminate the air.
3. Hose Maintenance
Inspect hoses for cracks or blockages. Regularly clean them to ensure they operate at maximum efficiency.
Future Trends in Industrial Vacuum Systems
The landscape of industrial vacuum systems is continuously evolving. Some trends to watch for include:
1. Automation Integration
As factories increasingly adopt Industry 4.0 practices, integrating smart technology with vacuum systems is becoming more prevalent. This includes remotely monitoring system performance and automating cleaning schedules.
2. Energy Efficiency
There is a growing emphasis on energy-efficient technologies that reduce power consumption while maximizing suction power.
3. Sustainability Practices
Many businesses are now focusing on sustainable practices. This includes using eco-friendly materials and designs that reduce environmental impact.
Conclusion
In conclusion, industrial vacuum systems are essential to maintaining a clean, safe, and efficient operational environment across various industries. By understanding their types, applications, and benefits, businesses can make more informed decisions regarding their implementation. Investing in the right system not only enhances productivity but also ensures compliance with safety regulations and contributes to long-term cost savings.
For businesses looking to optimize their manufacturing processes, exploring options for industrial vacuum systems is a significant step toward achieving operational excellence and sustainable growth.